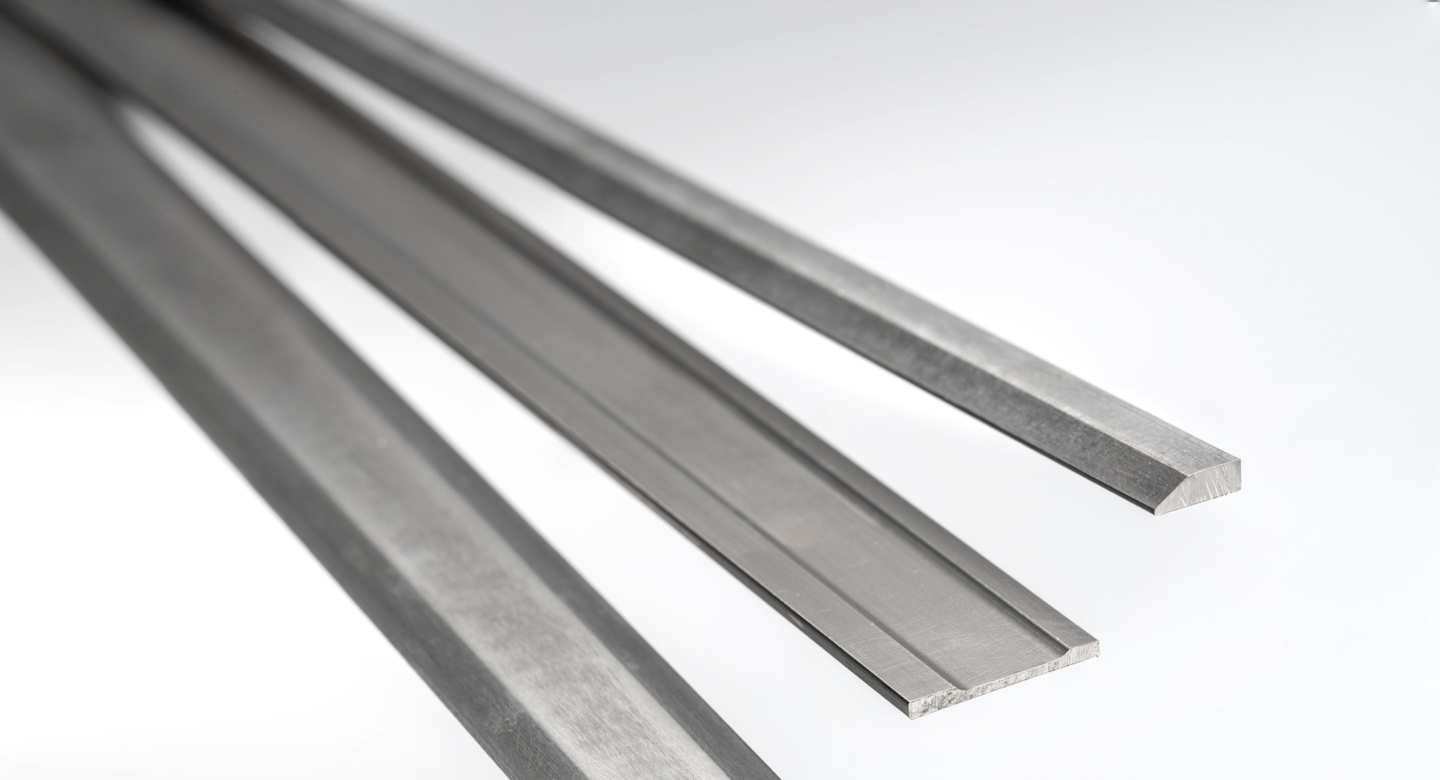
The Benefits of Shaped Wire for Stamped Parts Manufacturing
Starting with a shaped wire product can supplement stamping by pre-rolling in features to the material that otherwise cannot be stamped in. This is a tremendous advantage to stampers as using a pre-formed profile will allow the stamper to start with a near-net shape, potentially replacing some initial stamping or forming steps. Eliminating these steps could increase overall production yield by reducing processing time, tooling costs, and scrap.
The stamping process, also known as pressing, typically involves continuously running flat metal in coil form through a tool and die. The output of that process results in a stamped product manufactured to the specification needed for the part. In some cases, manufacturers will also utilize blanks for their production, which are also used for individual stamping.
A stamping press is designed specifically for stamping metal parts out of raw material, and upon running material, a tool and die will form the metal into a specified shape. Several types of stamping techniques may be used to achieve an end product, including punching, blanking, bending, coining, and more. Each of these processes can be effective in arriving at the desired shape, however, there are different cost variables involved with each.
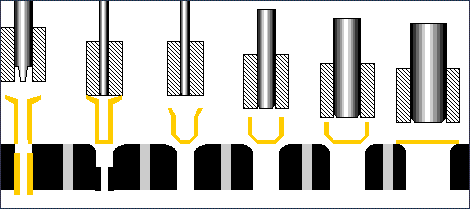
How Can Shaped Wire Benefit Stampers?
Starting with a Shaped Wire Product can supplement the stamping process by pre-rolling in features to the material that otherwise cannot be stamped in. This is a tremendous advantage to stampers as using a pre-formed profile will allow the stamper to start with a near-net shape, potentially replacing some initial stamping or forming steps. The elimination of these steps could increase overall production yield by reducing processing time, tooling costs, and scrap.
The Importance of Scrap Reduction
Today, far more manufacturers are focusing on reducing scrap from production. This is beneficial to the environment and the manufacturer's bottom line, while also giving customers the opportunity to see a reduction in cost and turnaround time which makes the manufacturer more competitive. As many stamping processes are multi-step, progressive processes, less scrap is typically produced when starting with a shaped wire product. Generally, using a shaped wire product can provide tighter tolerances over the alternative, which might help eliminate certain stages or steps in the stamping process that may otherwise be necessary when using regular flat material. This is possible through Ulbrich’s capabilities to pre-shape material.
At Ulbrich Shaped Wire, we produce a shaped material manufactured into its final profile by rolling round wire flat and then shaping the material by pulling or pushing the material through steel rolls. To start, we take round wire that progresses through the wire shaping process, where it is drawn down to what we require as our starting size. The drawing process elongates the wire and leaves an extremely low percentage of product leftover as scrap. This wire is then used to begin our rolling and shaping process. Fortunately, the overall scrap levels remain low, and this savings is essential as it helps provide our customers with the most competitive pricing we can offer.
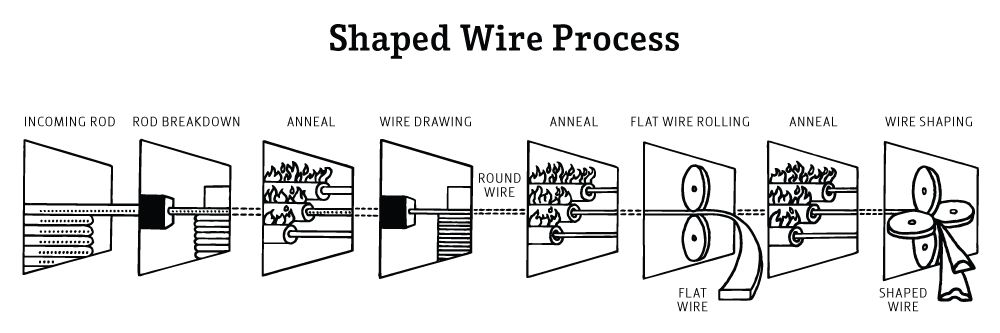
By combining this process with what a shaped or profiled product can offer, the stamper receives raw material that positions them very competitively once they begin running their jobs. This same benefit is afforded to our customers. When it hits their shop floor, the shape being near net allows them to avoid the scrap that would otherwise be produced by performing the operations to achieve the shape they need to start their manufacturing. This can be incredibly advantageous from a scrap prevention perspective but also has advantages in production speed.